Roller Granulator
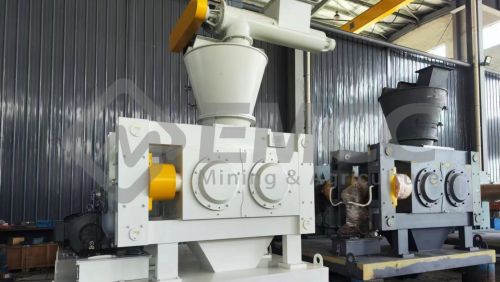
Roller granulator (Double Roller granulator) is a granulation equipment widely used in fertilizer, pharmaceutical, chemical and food industries. It applies high pressure through two relatively rotating rollers to press powdered or granular materials into dense flakes, and then forms uniform particles through a crushing and shaping process. Roller granulator is characterized by high efficiency, low energy consumption and suitability for continuous operation, and is particularly suitable for large-scale production. Its particle size and shape can be controlled by adjusting the distance between the rollers and the pressure applied. In addition, the roller granulator does not require the addition of binders, which is very suitable for materials that are sensitive to moisture and temperature. With its low operating cost and high production capacity, roller granulator excels in improving product quality and consistency, and is widely used in the production of high-quality fertilizer, pharmaceutical and chemical products.
What is the working principle of the roller granulator?
The working principle of the roller granulator is mainly to apply high pressure to the powder or granular material through two sets of relatively rotating rollers, press it into dense flake materials, and then form uniform particles through crushing and shaping processes. The following is the detailed working principle:
The raw material enters the roller gap of the roller granulator through the feeding device. The feeding device is usually equipped with a uniform distribution system to ensure that the material enters the roller evenly. After the material enters the roller, it is squeezed under high pressure under the action of the relative rotation of the two rollers. The high pressure makes the particles in the material closely contact and bond together to form a dense flake material. The surface of the roller usually has specific patterns or grooves to help the material form a specific shape and texture during the pressing process. After the pressed flake material is discharged from the gap between the rollers, it is initially crushed by the crushing device. The crushing device crushes large pieces of flake material into smaller particles. The particles after preliminary crushing enter the shaping device and are further homogenized through rolling, screening and other processes. The shaping device can adjust the size and shape of the particles as needed to meet specific product requirements. The final formed particles are discharged through the discharge port and enter the next process or are directly packaged. To ensure the quality and uniformity of the particles, screening is usually performed to remove unqualified particles that are too large or too small.
WE NOT ONLY PROVIDE RELIABLE PRODUCTS, BUT MORE IMPORTANTLY WE PROVIDE RELIABLE PROCESS DESIGN AND EXPERIMENTATION
WHAT MATERIAL CAN DOUBLE ROLLER GRANULATOR MAKING INTO FERTILIZER GRANULES?
Double roll granulator is a widely used equipment in fertilizer manufacturing process. It presses powdered or granular materials into dense flakes by applying high pressure to the materials, and then forms uniform granules through crushing and shaping processes. The following are some common materials that can be used for double-roll granulator, which can be used to make different types of fertilizer granules:
Nitrogen fertilizer
Urea: Urea is a high-nitrogen fertilizer. Urea powder can be pressed into granules by double-roll granulator, which is convenient for application and storage.
Ammonium nitrate: Ammonium nitrate has good hygroscopicity and can be granulated by double-roll granulator for fast-acting nitrogen fertilizer in agriculture.
Phosphate fertilizer
Monoammonium phosphate (MAP): Monoammonium phosphate is an important phosphate and nitrogen fertilizer. Its powdered material can be pressed into granules by double-roll granulator for easy application.
Diammonium phosphate (DAP): Diammonium phosphate can also be granulated by double-roll granulator and is often used in agriculture as the main phosphorus source fertilizer.
Potassium Fertilizer
Potassium chloride: Potassium chloride is the main raw material of potassium fertilizer. Its powdered material can be granulated by a double-roll granulator to increase the use efficiency of potassium fertilizer.
Potassium sulfate: Potassium sulfate is a high-quality potassium fertilizer, suitable for granulation by a double-roll granulator, and is used for crops that need potassium supplementation in agriculture.
Compound Fertilizer
NPK Compound Fertilizer: Compound fertilizer containing three nutrient elements of nitrogen, phosphorus and potassium. The mixed powdered material can be pressed into granules by a double-roll granulator to ensure uniform distribution of nutrients and facilitate fertilization.
Multiple trace element compound fertilizer: Through a double-roll granulator, a fertilizer mixture containing trace elements can be pressed into granules to provide comprehensive nutrition required by plants.
Organic Fertilizer
Compost: Through a double-roll granulator, fermented organic materials (such as livestock and poultry manure, crop straw, etc.) can be pressed into granules to increase the convenience and fertilizer efficiency of organic fertilizer application.
Biological Organic Fertilizer: Organic materials with beneficial microorganisms added can be granulated by a double-roll granulator to improve soil health and crop yields.
Other special fertilizers
Special fertilizers such as ammonium sulfate, ammonium nitrate and ammonium sulfate: These fertilizers can be granulated by a double-roll granulator to improve their physical properties and application effects.
Calcium magnesium phosphate fertilizer: This compound fertilizer contains calcium, magnesium and phosphorus elements, which is suitable for granulation by a double-roll granulator to improve the stability and uniformity of the fertilizer.
CONCLUSION
By using a double-roll granulator, these different types of fertilizer raw materials can be effectively converted into uniform particles, improving the use efficiency and application convenience of fertilizers, and meeting the nutritional needs of different crops.
EMCC granulators are carefully designed to meet specific processing goals and are available as stand-alone units or as part of a complete granulation line. In addition to the world’s most prestigious granulators, EMCC also provides feasibility and process development services, as well as parts and service support. To learn more about our roller granulators, contact us today!
WE NOT ONLY PROVIDE RELIABLE PRODUCTS, BUT MORE IMPORTANTLY WE PROVIDE RELIABLE PROCESS DESIGN AND EXPERIMENTATION
What granulation method does the double-roll granulator use? What are its advantages?
The double roller granulator uses the dry granulation method. This method directly presses powdery or granular materials into dense flake materials through mechanical pressure, and then crushes and screens these flake materials into uniform particles.
Advantages
Energy saving and environmental protection
Dry granulation does not require the addition of liquid binders, is suitable for materials that are sensitive to moisture and temperature, and reduces the drying and liquid handling steps.
Since there is no need to humidify and dry the materials, energy consumption is reduced, which helps to reduce production costs and environmental impact.
High efficiency
The double roller granulator can produce a large number of uniform particles in a short time, improves production efficiency, and is suitable for large-scale continuous production.
The equipment is simple to operate and has a high degree of automation, which reduces the requirements for operator skills and is easy to manage and maintain.
Strong adaptability
It can handle a variety of materials, including various fertilizers (such as nitrogen fertilizers, phosphate fertilizers, potash fertilizers, compound fertilizers), drugs and chemical raw materials, especially those that are difficult to granulate by wet methods.
By adjusting the roller spacing and pressure, particles of different specifications and shapes can be produced to meet different product requirements.
Low operating cost
The equipment has a simple structure, durable parts, and convenient maintenance, which reduces the operating and maintenance costs.
Dry granulation reduces the waste liquid and waste gas generated in wet granulation, and reduces the waste treatment and environmental protection costs.
High product quality
Through high-pressure extrusion and crushing shaping process, the particles produced are of uniform size and stable quality, which is conducive to improving product consistency.
By adjusting the equipment parameters, the density and hardness of the particles can be controlled to meet the requirements of different applications.
Reduce waste
The utilization rate of materials in the dry granulation process is high, which reduces material waste and reduces production costs.
Dry granulation reduces the waste liquid and waste gas treatment problems that may be generated in wet granulation, reduces environmental pollution, and meets environmental protection requirements.
Improve nutrient utilization rate
In fertilizer production, the double-roll granulator can improve the nutrient content and utilization rate of fertilizer particles, enhance fertilizer efficiency, and meet the needs of modern agriculture for efficient and environmentally friendly fertilizers.
Conclusion
Through these specific advantages, the double-roll granulator has been widely used in a variety of industries and has become an indispensable and important equipment in modern industrial production.
EMCC granulators are carefully designed to meet specific processing goals and are available as stand-alone units or as part of a complete granulation line. In addition to the world’s most prestigious granulators, EMCC also provides feasibility and process development services, as well as parts and service support. To learn more about our roller granulators, contact us today!
WE NOT ONLY PROVIDE RELIABLE PRODUCTS, BUT MORE IMPORTANTLY WE PROVIDE RELIABLE PROCESS DESIGN AND EXPERIMENTATION
How the Double Roller Granulator Works in Your Fertilizer Granule Production
The working process of the double roll granulator in the production of fertilizer granules can be specifically divided into the following steps:
Material preparation
Powdered or granular raw materials (such as urea, diammonium phosphate, potassium sulfate, etc.) are mixed in a certain proportion, and binders or other additives are added as needed. These raw materials usually go through a drying and mixing process to ensure their uniformity and appropriate moisture content for the subsequent granulation process.
Feeding system
The mixed material is evenly fed into the feeding port of the double-roll granulator through a feeding device (such as a screw conveyor or a vibrating feeder). The feeding system can adjust the feeding speed of the material to ensure that the material enters the granulator continuously and stably.
Extrusion molding
The material entering the granulator is extruded between two relatively rotating rollers. The surface of the roller is usually engraved with mold grooves of specific shapes, which determine the shape and size of the final particles. The rotation and high pressure of the rollers compact the material in the mold grooves and form particles.
Cutting and cooling
The pellets after pressing are usually long strips and need to be cut into small pellets of the required length by a cutting device. The cut pellets are cooled by a cooling system (such as a cooling belt or cooling drum) to harden the pellets and improve their strength. During the cooling process, the moisture content of the pellets is further reduced to improve the storage stability of the product.
Screening and grading
The cooled pellets are graded by screening equipment to remove unqualified pellets and fine powder. Qualified pellets are graded according to size to ensure the consistency and quality of the product.
Packaging and storage
Qualified pellets that have been screened and graded are sent to the packaging system for automatic packaging. The packaged fertilizer pellet products can be directly stored or transported to the market for sale.
Main technical parameters
Roller pressure: affects the density and strength of the pellets, and can usually be adjusted to meet the needs of different materials.
Roller speed: affects production efficiency and pellet quality, and needs to be adjusted according to production requirements.
Mould groove shape: determines the shape and size of the pellets, and different molds can be customized according to market demand.
Equipment features
High efficiency: can continuously and stably produce high-quality pellets with high production efficiency.
Energy saving: Compared with other granulation methods, the double roller granulator has lower energy consumption.
Easy operation: The equipment has a simple structure, convenient maintenance, and low operator training cost.
Good product quality: The particles are uniform, high in strength, and suitable for long-term storage and transportation.
Conclusion
Double roller granulator is widely used in agriculture, chemical industry and other fields in the production of fertilizer particles due to its high efficiency, energy saving, easy operation and good product quality, meeting the market demand for high-quality fertilizer products.
EMCC granulators are carefully designed to meet specific processing goals and are available as stand-alone units or as part of a complete granulation line. In addition to the world’s most prestigious granulators, EMCC also provides feasibility and process development services, as well as parts and service support. To learn more about our roller granulators, contact us today!
WHY CHOOSE EMCC AS YOUR PARTNER?
Shanghai Exceed Industry Co., Ltd (China EMCC) is a manufacturing enterprise specializing in high-tech fertilizer machinery. For many years, we have devoted to producing inorganic and organic fertilizers granulator equipments. By consistently creating values for our customers around the world, we have become one of the leading suppliers in global agricultural fertilizers industry. With China EMCC, you may get comprehensive services of consulting, design, equipment, installation, training, emergency assistance, field assistance, spare parts and routine maintenance to save fertilizer plants cost.
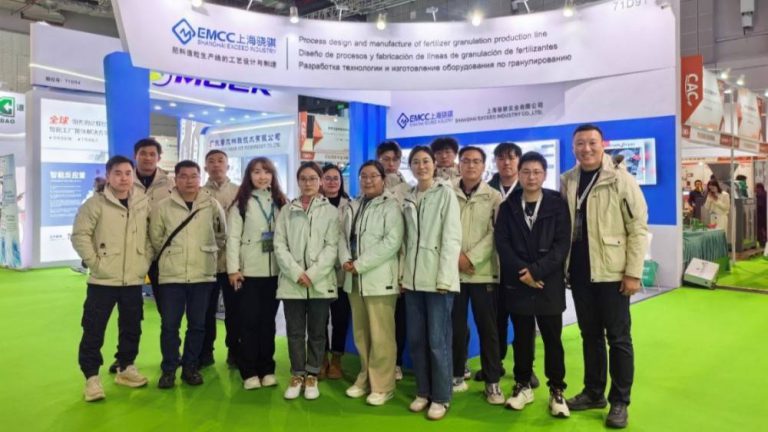
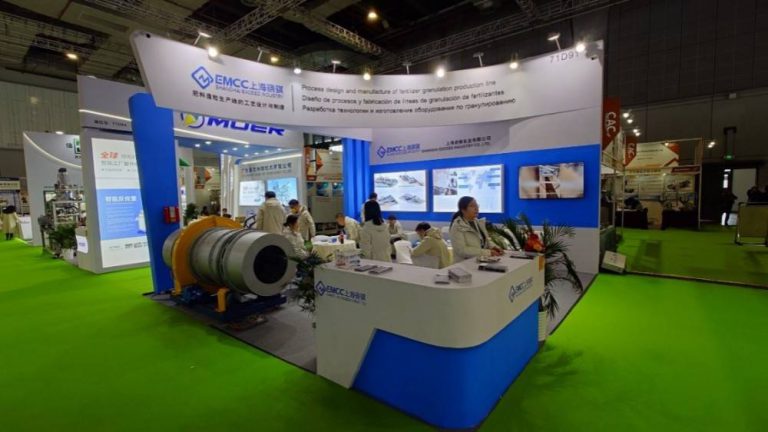

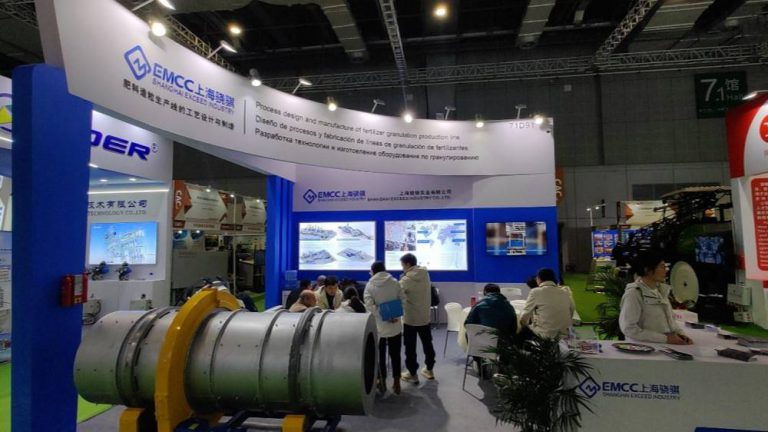
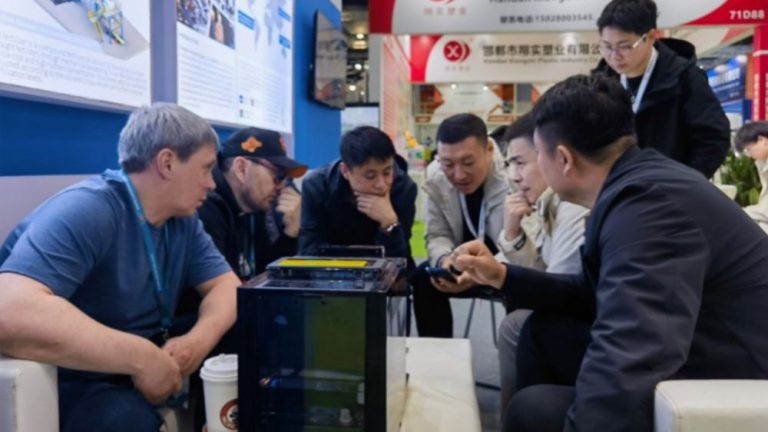

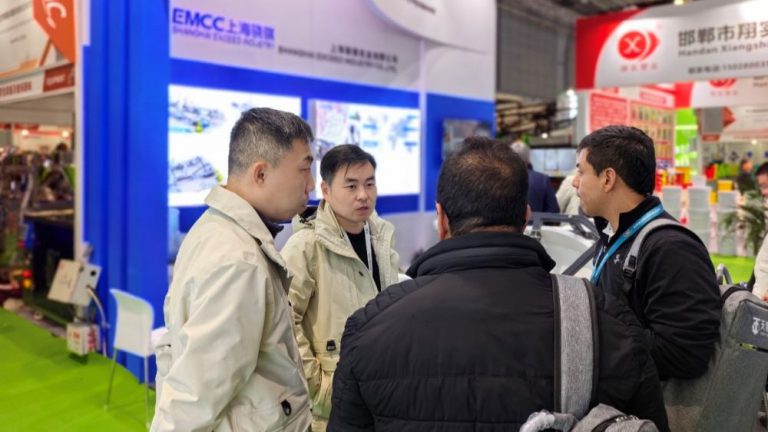
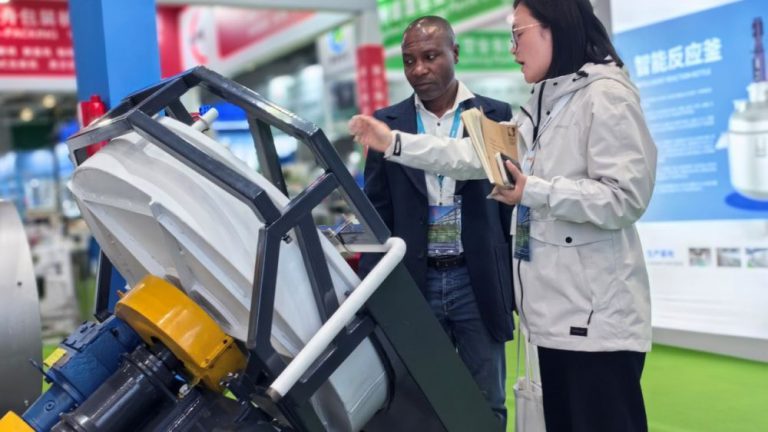
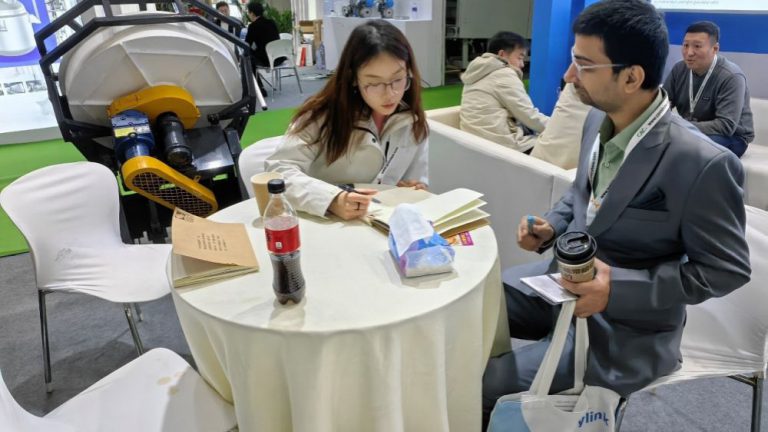
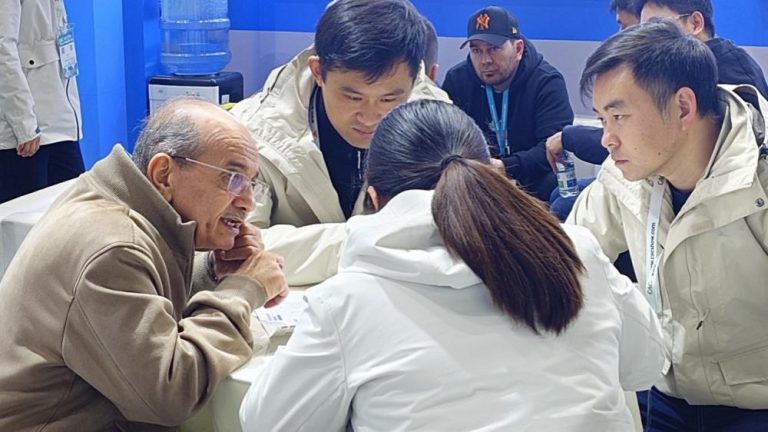
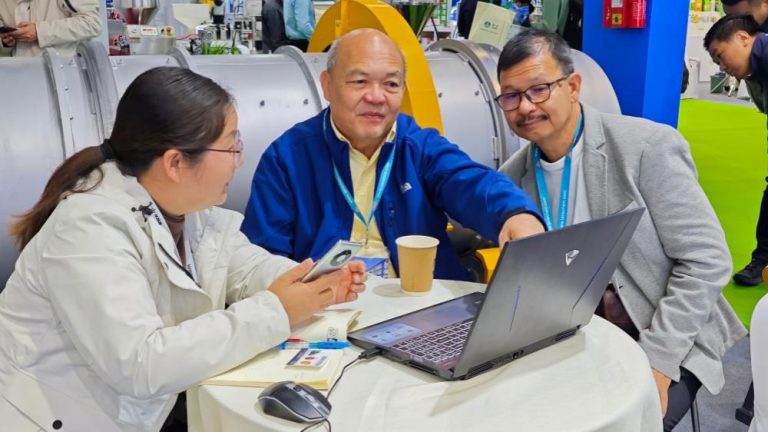